Enabling shop floors
go Lean.
What we do
We empower decision makers at all levels in manufacturing plants to get real time data from machines at their fingertips, wherever they are, at any time, on any device. This enables them to cut waste of machine capacity, material and manpower, and thereby improve profits.
Why we do this
Inaccurate & late data = Wrong decisions or No decisions
30-50% machine capacity utilization is common in manufacturing shop floors. This is because the traditional machine monitoring system is dependent on a chain of humans with data recorded on paper and transferred to computers once a shift. Decision makers get the data after 24 to 48 hours. The data is not accurate, and arrives too late to take action if there are crisis situations.
For decision makers in a firm to be able to take proper decisions, the production monitoring system must give them accurate and timely (as in instantaneous) data from machines. Only a machine monitoring system based on Industry 4.0 can do this-Hence Leanworx. A manufacturing monitoring system for SMEs that not only makes sense, but is an absolute necessity to run profitably.
Leanworx: Where accurate, real-time data meets decisive action.
Have we succeeded?
We think YES, BRILLIANTLY.
Leanworx improves profits dramatically, in just weeks. By giving accurate data from machines, in seconds.
The benefit to cost ratio varies from 5 to 20, depending on the cost of the machine
Our smallest customer has 7 machines. Our largest customers are India’s top manufacturers of automobile parts, aerospace parts, purtips, springs, etc.
These are the benefits they have seen.
Our business and Design philosophy
Demystify and simplifying Industry 4.0 for all industries, from SMEs to large corporations.
Minimizing costs-direct and indirect-for system acquisition and maintenance. Ensure user-friendliness for all personnel, from machine operators to CEOs Monitor machines of any age with any level of electronics, or no electronics. Monitor diverse processes in discrete manufacturing (metalworking, packaging. food, pharma, plastics).
Replace manual data tasks with Al-driven collection, analysis, reporting, and alerts.
Cementing our position
Leanworx firmly secured its place in the machine monitoring systems landscape by winning the esteemed FIE Foundation award at IMTEX 2018, one of the world’s premier manufacturing trade shows. This accolade, recognizing Leanworx as the most innovative product, is as a resounding testament to the company’s pioneering approach. Remarkably, this achievement unfolded within a mere 8 months since Leanworx embarked on its journey. It serves as a powerful affirmation of the company’s disruptive use of technology to elevate machine efficiency. This rapid recognition showcases not only Leanworx’s commitment to innovation but also its capacity to swiftly make a substantial impact in the dynamic realm of machine monitoring systems.
Mission:
Empowering discrete manufacturing shop floors to go Lean, by delivering actionable insights on machine waste through Industry 4.0.
Vision:
Facilitating global shop floors to achieve more with less through a plug-and-play, affordable, and user- friendly machine monitoring system.
The
Team
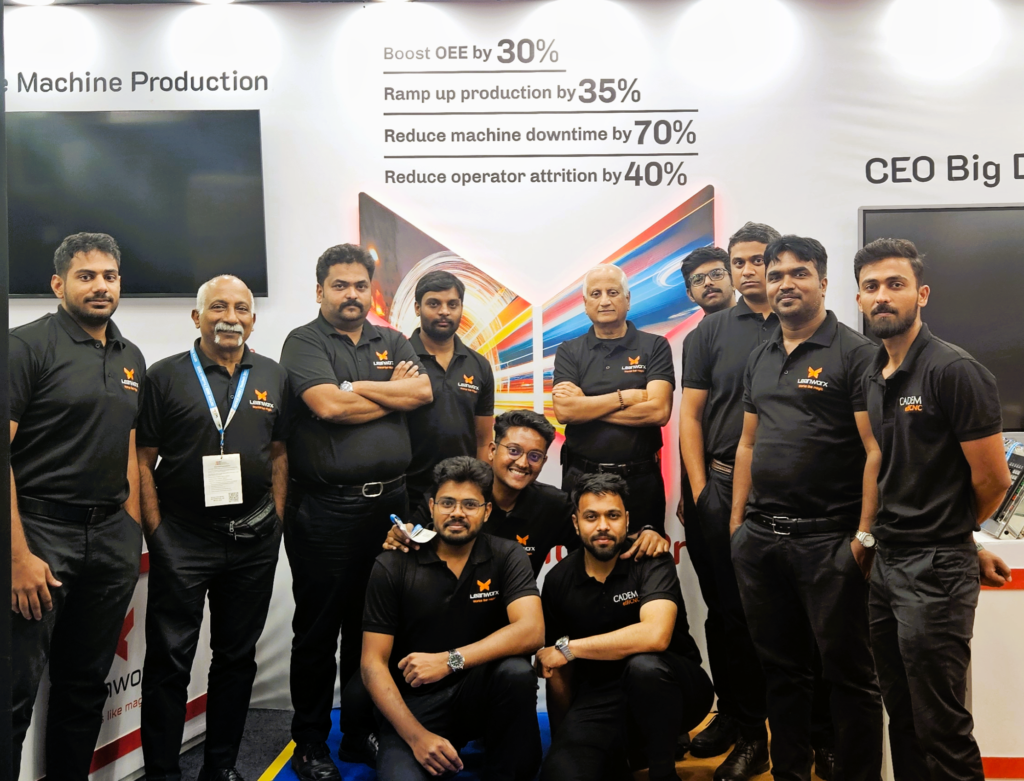
Meet the dedicated individuals at Leanworx who orchestrate your productivity improvement. From visionaries shaping the future to hands-on implementers making it happen – our team comprises experts and doers, each playing a crucial role in ensuring that you get the best from our product.
Strategy specialists
With a background in running CNC machine shops in the production of earthmover, aerospace, and tooling parts, Dasarathi is well-versed in CNC programming, tooling, and scheduling. His expertise extends to the architecture, testing, and support of CAD/CAM, DNC, and Industry 4.0 systems. Having navigated the intricacies of the manufacturing landscape, he is a seasoned professional whose multifaceted skill set contributes significantly to the vision and success of Leanworx.
With a versatile career journey, Srihari has excelled in press tools design, forklift sales, and Sales and Marketing roles for both CAD/ CAM software and Industry 4.0 systems. His comprehensive expertise, spanning from precision engineering to cutting-edge IT in manufacturing, positions him as a pivotal force in driving Leanworx’s success in sales and business development. Srihari’s strategic acumen and proven track record make him an invaluable leader in our journey toward excellence.
Bhagavan’s extensive experience includes providing support for CAD/CAM software, as well as spearheading the design and development of CAD/CAM software, DNC software, and Industry 4.0 systems. His deep expertise in software development is instrumental in shaping Leanworx’s innovative solutions. His commitment to excellence and technical prowess make him a driving force in steering Leanworx towards continuous innovation and cutting-edge advancements.
Execution specialists
A seasoned Sales Engineer and South Region Sales Manager, Sandesh leads sales for South India . With a robust background in the computer software industry, he excels in Production Management, Sales, Pricing Strategy, and Direct Sales of Industry 4.0 solutions and CAD/CAM. A results-driven professional with a Bachelor of Engineering degree, he brings strategic leadership to our team, steering Leanworx towards continuous growth and success.
With a specialized focus on Industry 4.0, Kaushik brings valuable experience in the installation, testing, and support of both software and hardware within this transformative realm. His expertise is in shop floor analytics, waste detection, product design and testing of Industry 4.0 systems. Kaushik’s contributions play a crucial role in ensuring the seamless integration and functionality of our solutions, ultimately contributing to Leanworx’s mission of optimizing manufacturing operations through cutting-edge technologies.
A key player in our Software Development team, Shyamaraj is responsible for making Leanworx the market leader in terms of innovation, ease of use and reliability. He brings his earlier hands-on experience experience in installation, testing, and support of Industry 4.0 systems to developing Leanworx’s great front and back end, and innovative AI-driven data collection and analytics engines.
Ananda P. is a valuable member contributing to our financial operations at Leanworx. He plays a crucial role in ensuring the financial integrity and compliance of our organization. His meticulous attention to detail and financial acumen contribute to the smooth functioning of our financial processes, reinforcing Leanworx’s commitment to operational excellence in all aspects of business management.
Our
Speak
Customers
Our clientele includes some of the most prominent names in the manufacturing industry. Hear firsthand from leaders who have experienced the transformative power of our solutions.
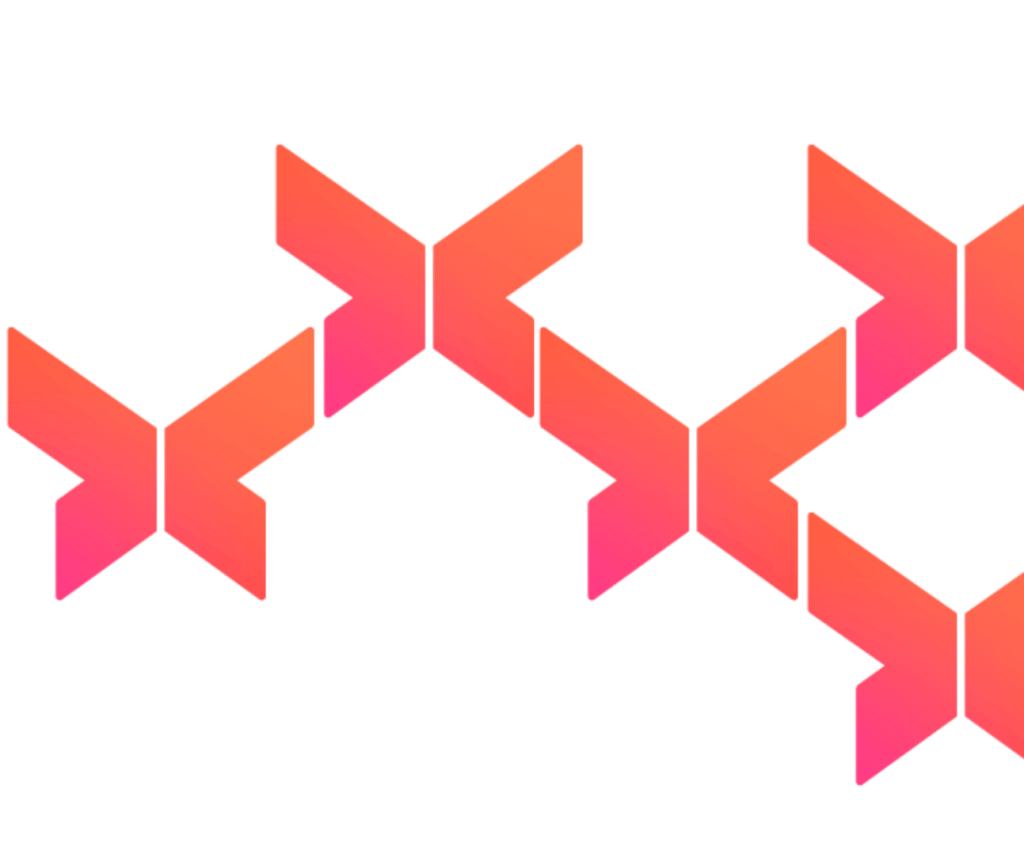
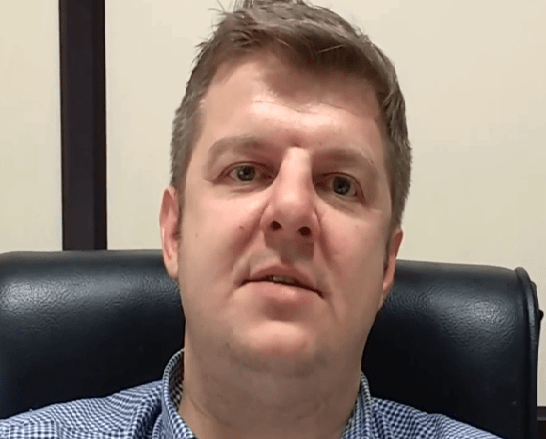
Gavin Price
MD Aaran Engineering
We’ve seen a lot of OEE improvements because now we can understand the parts, the spindle runtime, how effectively we are. It’s actually helped us to move from three shifts down to two shifts with more output. So we’ve taken from about 30% spindle utilization to now over 55% spindle utilization. It’s allowed us to put a bonus structure in place which is monitorable.
We’ve been extremely happy with the way that they’ve worked, which is coming from the way that the utilization of the machines has improved. Our downtime has decreased by 10%. The downtime, especially in the night shift, has reduced by more than 25%, which is a very, very important thing for us and is contributing a lot towards our productivity. So I would definitely recommend leanworks to others who are doing CNC machining like we are. We are spread over four plants, but can control them all from our office, looking at the data, getting information real time, getting updates and reports every day.
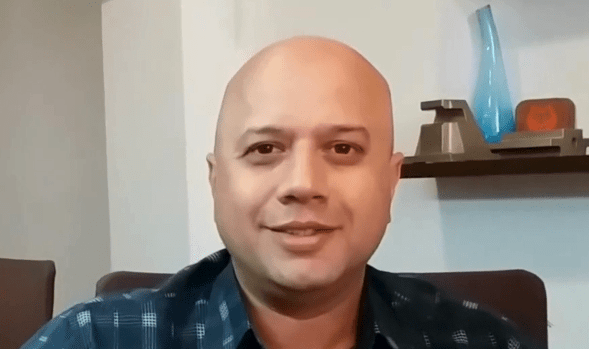
Deepak Pinto
MD, Zenith Precision
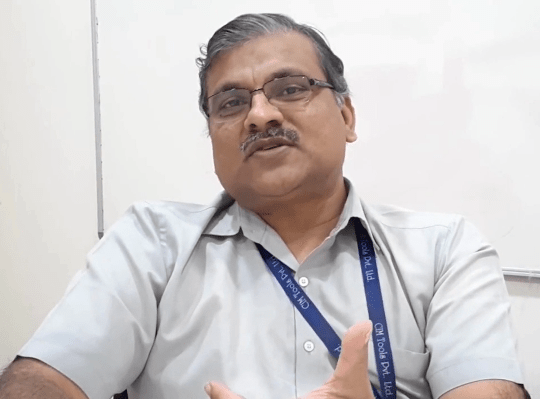
B.T. Umesh
DGM, CIM Tools
So overall, I see at least eight to 10% of efficiency improvement with this, especially OEE and the spindle run. Spindle run is effective utilization of spindle run. There are a lot of idle times that was there. Setup time was reduced. We can see there is an improvement of at least ten to 12% of production improvements. Just you put a monitoring. Then the discipline came into picture. Further details has come out and identified the root causes. And then we improve the efficiencies. That’s how we have implemented, thanks to Leanworx.
Leanworxs we have been able to bring down our machine downtime by about 30% and the increase in OEE by 10% which ten to 15%, which is a huge saving. Now we plan to connect all the 24 machines we have through leanworxs and have a comprehensive data on that. We have been getting fantastic results out of it. The reports that we generate every morning gives us a good insight on the productivity and the performance of the operator as well as the machine. I recommend it highly to all the manufacturers who have CNC setups or any machines that can be fitted with this.
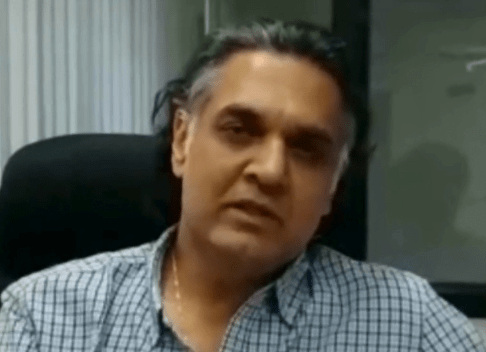
Sanjay Desai
CEO, RBD Engineers
The quality of data, accuracy of data, timeliness of the data is very, very important. That’s how Leanworxs is helping implementing leanworxs we are no longer discussing the quality of data accuracy of data. Discussion revolves around what can be done to improve the productivity. Looking at the benefit of utilizing and improving the equipment due utilization, the incremental cost. What we incur by paying the subscription is very small and it’s a good value proposition from our point of view.
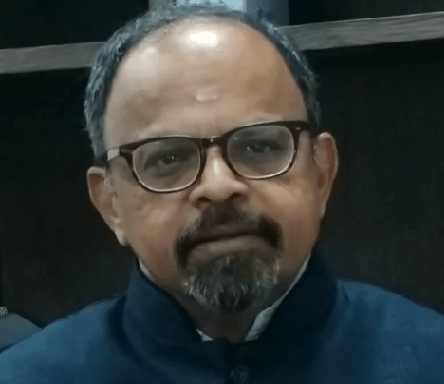
L Krishnan
MD, TaeguTec India
Gavin Price
MD Aaran1 Engineering
We've seen a lot of OEE improvements because now we can understand the parts, the spindle runtime, how effectively we are running. It's actually helped us to move from 3 shifts down to 2 shifts with more output. So we've moved from about 30% spindle utilization to now over 55% spindle utilization.
Our downtime has decreased by 10%. The downtime, especially in the night shift, has reduced by more than 25%, which is a very, very important thing for us and is contributing a lot towards our productivity.
Deepak Pinto
MD Zenith Precision
Overall, I see at least 8 to 10% efficiency improvement, especially OEE and the spindle run time. Setup time has been reduced and we can see an improvement of at least 10 to 12% production improvement.
B.T. Umesh
DGM, CIM Tools
It takes hardly 10 minutes for a person to connect to the machine. I can tell you that we are able to reduce the downtime, and we are able to improve productivity. The middle level supervisors and managers are also satisfied with the exact data that they are getting from the Leanworx system.
Gurpreet Singh
MD, Pal Shell Cast
With Leanworx we have been able to bring down our machine downtime by about 30% and increase in OEE by 10 to 15%, which is a huge saving. We have been getting fantastic results out of it. The reports that we generate every morning give us a good insight on the productivity and the performance of the operator as well as the machine.
CEO,RBD Engineers
Sanjay Desai
L Krishnan
After implementing Leanworx we are no longer discussing the quality of data or accuracy of data. Discussion revolves around what can be done to improve productivity. Looking at the benefit of utilizing and improving the equipment utilization, the incremental cost that we incur by paying the subscription is very small and it's a good value proposition from our point of view.
MD, TaeguTec India
Anil Machani
When a customer asks, What is your OEE? We say 85%. Are we really at 85%? I don't think so. After installing Leanworx and improving systems, it's 88 when we finally checked the last time. So that's a substantial advantage.