OEE monitoring systems – why cooking up OEE is a bad idea
- Sep 9, 2023
Category : OEE monitoring systems
- OEE monitoring systems – why cooking up OEE is a bad idea
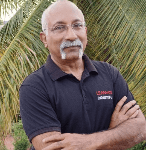
Dasarathi G V
Director in Leanworx
Dasarathi has extensive experience in CNC programming, tooling, and managing shop floors. His expertise extends to the architecture, testing, and support of CAD/CAM, DNC, and Industry 4.0 systems.
Try Leanworx for free
- In OEE monitoring systems, it is important that you are truthful about losses like downtimes, rejections and rework in the OEE calculation formula.
- OEE is not a number that you flaunt to others. It is a mirror that helps you evaluate and improve the performance of your shop.
- OEE is a number that you constantly strive to improve, not a number that you achieve and then sit back and relax.
- This is why a cooked up OEE calculation formula makes no sense.
OEE tracking system - results of cooking up OEE
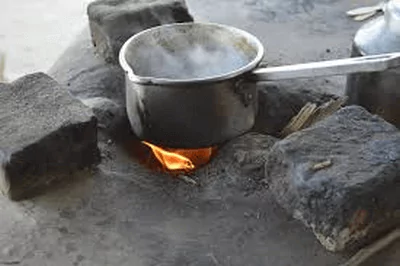
The easiest cooking up method - ignore some downtimes
A lot of firms consider most downtimes reported by the OEE tracking system as part of the process, and NOT as downtimes. E.g., part unloading / loading, inspection, setup change. This flies against the logic of OEE calculation. It artificially inflates the OEE number, and can cause great harm.
Availability is defined as = Run time / Planned production time.
Run time = Planned production time – Downtime.
Downtime is the time when the process was supposed to be running but did not run. This includes part unloading and loading, inspection, setup changes, breakdowns, etc.
Here’s why you must consider ALL downtimes as downtimes
You can get an artificially high Availability of 95 % by excluding some down times, and making the numerator in the Availability equation go up. However, if you do this, you’ll just assume that there is very little further improvement possible, and just sit back and relax. Let’s say the setup time for a part on a CNC lathe is 2 hours. If you do not consider this as downtime, this setup time is going to remain constant for years together. If you do consider it as downtime, you’ll keep on trying to reduce it, by using quick change tooling, automatic tool presetter, etc. Similarly for other downtimes. The fact is that there is only one OEE calculation formula for calculating Availability, Performance, Quality and OEE. However, a lot of firms define their own OEE formulae, to get OEE numbers to suit their own taste.
OEE is a single number that shows you the capacity utilization of your machine. It enables you to measure and reduce waste (of available time, machine capacity, raw material) on the shop floor. It is a single number that you can communicate to, and is understood by, everybody from the machine operator to the CEO.
OEE = Availability x Performance x Quality
The components Availability (A), Performance (P) and Qquality (Q) in the OEE formula can be summed up as representing:
1. How much time did the machine run ?
2. How efficiently did the machine run ?
3. What was the quality of the parts ?
Availability: This is the ratio of the time that the machine ran, to the time that it could have run. The difference is the idle time caused by breakdowns, setup, shift-change, etc.
Performance: This is the ratio of the number of parts produced, to the number of parts that theoretically could have been produced. The difference could be because of slow part unload and load, higher cycles times, etc. On a CNC machine, the difference could be because of use of feed rate override.
Quality: The ratio of the number of parts that are of acceptable quality to the total number of parts made. The difference is the number of rejected parts.
Start using Leanworx for free
We provide a 5-day free demo, with assistance in installation and usage.
OEE tracking software – recipes for cooking up OEE
The OEE calculation formula can be modified in various ways to cook up good looking OEE numbers in the OEE tracking software. Here are some recipes, and what each dish tastes like.
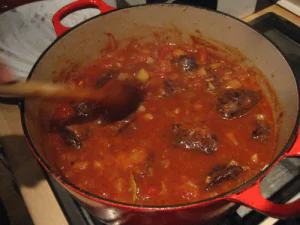
OEE calculation cooking up - Recipe 1
In Availability in the OEE calculation formula, do not consider setup change times as downtime, because “How can you consider this a downtime ? After one batch of parts is done, you have to do a setup change and it takes time, right ? So it’s actually part of the cycle”. The taste: Maybe you can reduce a 2 hour setup time to 15 minutes by the use of quick change tooling, or by using a tool presetter, or by work and tool offset probes. You’ll never do this, because you have hidden this downtime waste forever and will never know that it exists.
OEE calculation cooking up - Recipe 2
In Performance in the OEE calculation formula, make the part change time a part of the cycle time, because “How can you consider this a downtime ? You have to unload the completed part and load a new part, right ? So it’s actually part of the cycle”. The taste: Maybe you can reduce the part change time by using a pallet changer, or with better and faster clamps on the fixture, a better and faster crane, or a robot. You’ll never do this, because you have hidden this manufacturing downtime waste forever and will never know that it exists.
OEE calculation cooking up - Recipe 3
In the Availability part of the OEE calculation formula, do not consider chip cleaning, insert changing and part inspection times as downtime, because “All these are part of the process. They are not downtimes.” The taste: Maybe you can eliminate the chip cleaning time by using better chip breaker geometry and cutting parameters, reduce the frequency of insert changes by using an insert with a better life. Maybe you can speed up the inspection or reduce its frequency. You’ll never do this, again because you have hidden these downtime wastes in manufacturing forever and will never know that they exist.
OEE monitoring system - be truthful with downtimes in the OEE
As you can see, the taste in all these recipes is uniformly bad. These are only some examples of bad practices in the OEE calculation formula. There really is no point in hiding downtimes to inflate OEE numbers. This comes from an obsession with the absolute value of the OEE. Instead, use it as a measure of productivity that needs to be improved. Set a target for periodic improvement, not an absolute value. Just let ALL the downtimes be visible, out there, so that you will keep reducing them and never forget them.
This is the key tenet of LEAN – be honest about the wastes reported by your OEE monitoring system. Do not hide them.
Keep Learning
Increase your profits automatically. Use Leanworx to get accurate and instant data 24/7.
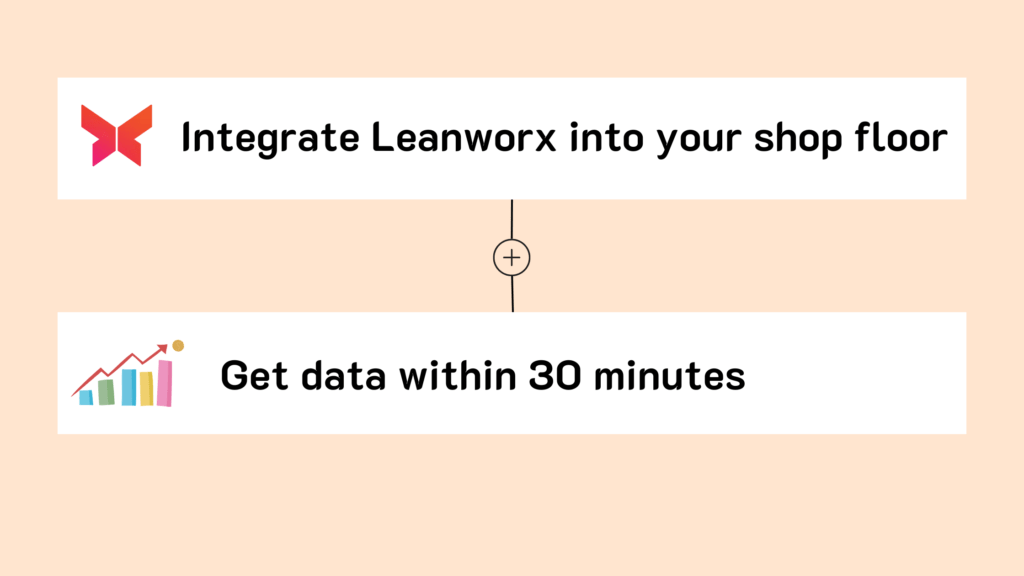