Is manufacturing monitoring system useless in SMEs ? [ Misconception Explained]
- Mar 19, 2024
Category : Production monitoring systems
- Is manufacturing monitoring system useless in SMEs ? [ Misconception Explained]
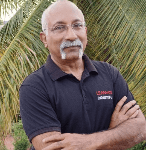
Dasarathi G V
Director in Leanworx
Dasarathi has extensive experience in CNC programming, tooling, and managing shop floors. His expertise extends to the architecture, testing, and support of CAD/CAM, DNC, and Industry 4.0 systems.
Try Leanworx for free
- A manufacturing monitoring system in SMEs yields big benefits in profits.
- It is very affordable.
- It pays back for itself in 1 or 2 months.
- Industry 4.0 is primarily data collection directly from machines, followed by analysis, and action/reporting.
- The key components are a sensor that collects data from the machine, IOT and Cloud computing.
- None of these is high tech or expensive today.
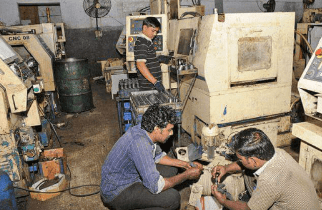
Problems in SMEs, fixed by Manufacturing monitoring systems
If you’re the owner of an SME manufacturing firm, these are probably your problems.
You run the firm yourself, with no management hierarchy. Productivity is high when you are in the shop. When you are not, machines are idle a lot and production is low. You however cannot be present all the time. You have a lot of other work to do outside, like meeting customers and vendors, going to the bank, going to providers of government services like the electricity provider or the tax offices.
The first shift is supposed to start at 6 AM, but the machine is only switched on at 6:30. Lunch and tea breaks extend 15 minutes beyond their scheduled times. Night shift production is always low. There are frequent complaints of power shut down or machine breakdowns, no raw material, no tools. Of these, some are systems issues and some are work ethics issues. Your machines are typically down 30 to 50 % of the time. You know that utilization is bad, but you don’t know the exact extent of machine downtimes or their reasons.
A manufacturing monitoring system gives you this data 24/7, on your laptop or tab or mobile phone, even when you are not present in your shop floor.
Types of production monitoring system benefits
A production monitoring system enables you to know exactly what is happening on the shop floor. You can know the production quantity on each machine at any instant, the extent of machine downtime and the causes of downtimes. You can focus on the biggest downtimes, fix the issues and improve profitability. All this without even going to the shop floor. You can track machines from anywhere, at any time, on your mobile phone, tablet or laptop.
Some of the benefits are:
– Produce more and earn more with the same number of machines, improve profits dramatically.
– Improve production quantities.
– Reduce capital expenditure on new machines.
– Reduce rejections.
– Reduce consumables usage (inserts, coolant, power, etc.).
– Cut down the number of shifts to produce the same quantity.
– Ensure that production is uniform through the day, without being physically present on the shop floor.
Simple logic: If you have a downtime of 40% and manage to cut this down to 20%, this means your 5 machines have now become 6 machines without actually buying another machine.
Start using Leanworx for free
We provide a 5-day free demo, with assistance in installation and usage.
Real life benefits - manufacturing production monitoring system
Here are some case studies of benefits that firms using Leanworx have actually seen :
1. CapEx reduction – no new machines purchased for 2 years. View case study
How a firm increased capacity by reducing machine downtime, and froze capital expenditure on new machines for 2 years, even though their orders were increasing.
2. Eliminated late starting and early stoppage. View case study
Downtime in a shop was 1 hour in each shift of 8 hours (12.5 % of the total time) due to late starting and early stopping . This was completely eliminated after Leanworx was installed.
3. Firm reduced 3-shifts working to 2-shifts working. View case study
How a firm made the same number of parts in 2 shifts, that they were making in 3 shifts earlier. Saved on personnel costs, power, etc.
It does not matter whether a firm has 3 machines, 30 machines or 300 machines. The benefits are the same.
Manufacturing production monitoring system benefits in SMEs – cost
There are Industry 4.0 systems available that come for as low as Rs. 1000 per month, or Rs. 25,000 one-time. If your machines costs Rs. 200 an hour and your downtime is the typical 40 % of a possible 22 hours, you’re losing Rs. 1760 a day. Even if you reduce your downtime losses by 25 %, your benefit is Rs. 440 per day., or Rs. 20,000 per month. This is easily achievable in just 1 month. Downtime due to work ethics issues (late start at shift start, early stoppage at shift end, extended lunch breaks, etc.) alone typically account for 12 % of the total available time, between 2 to 3 hours a day. This will reduce to almost zero in just 2 weeks.
Manufacturing production monitoring system benefits in SMEs – time to install
There are plug-and-play Industry 4.0 systems that can be connected to your machine in just half an hour, by the person who normally maintains your machines. The moment this is done, you can start seeing reports on your mobile phone, tab or PC from anywhere at any time. You can be sitting at home, waiting at a customer’s office, out of town, or anywhere. You can see what is happening on your machines 24 hours, and take immediate action. You get alerts on your mobile phone for burning issues – machine breakdown, abnormal downtime, shift production below target, etc.
Leanworx, is a plug-and-play system for SMEs, based on Industry 4.0. It is very affordable, and pays back for itself in just a month. It takes about 15 minutes to connect to each machine, and you can start seeing reports and getting alerts immediately.
A manufacturing monitoring system for SMEs not only makes sense, it is an absolute necessity to run profitably.
Keep Learning
Increase your profits automatically. Use Leanworx to get accurate and instant data 24/7.
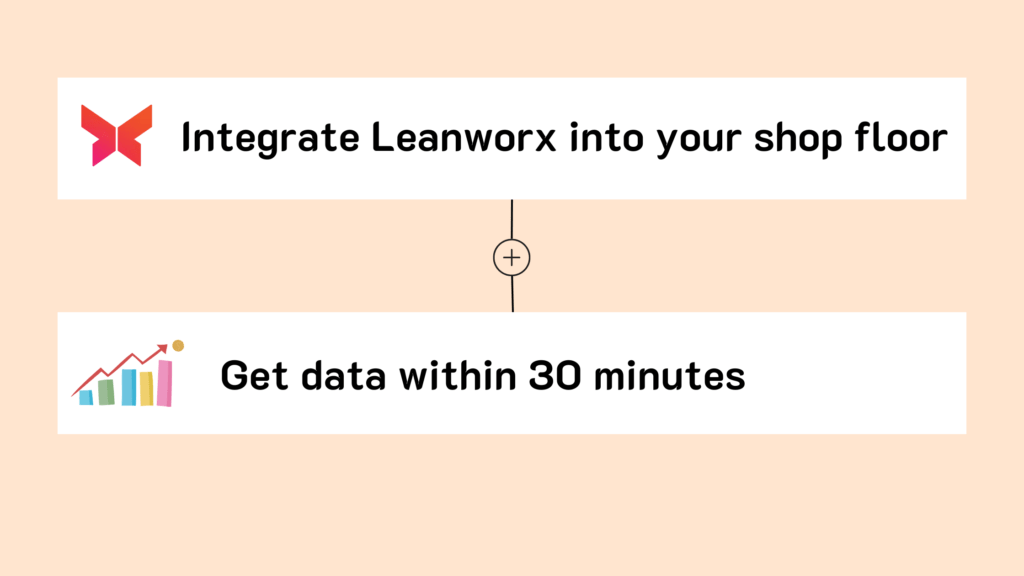