How manufacturer of machined castings for export saved Rs . 5.6 crores CapEx
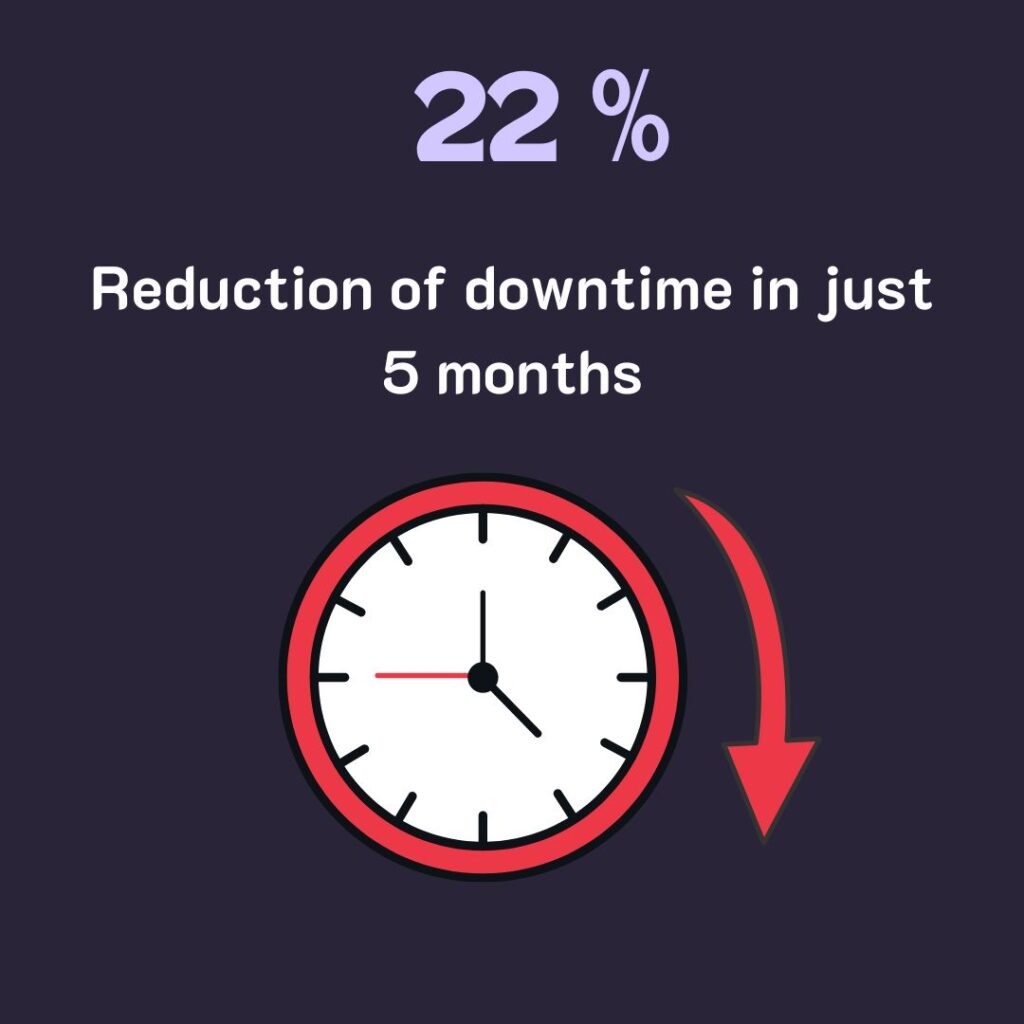
22 % reduction of downtime in just 5 months
The company successfully reduced downtime to 22% within a short span of 5 months, with sustained improvements in the subsequent 2 years.
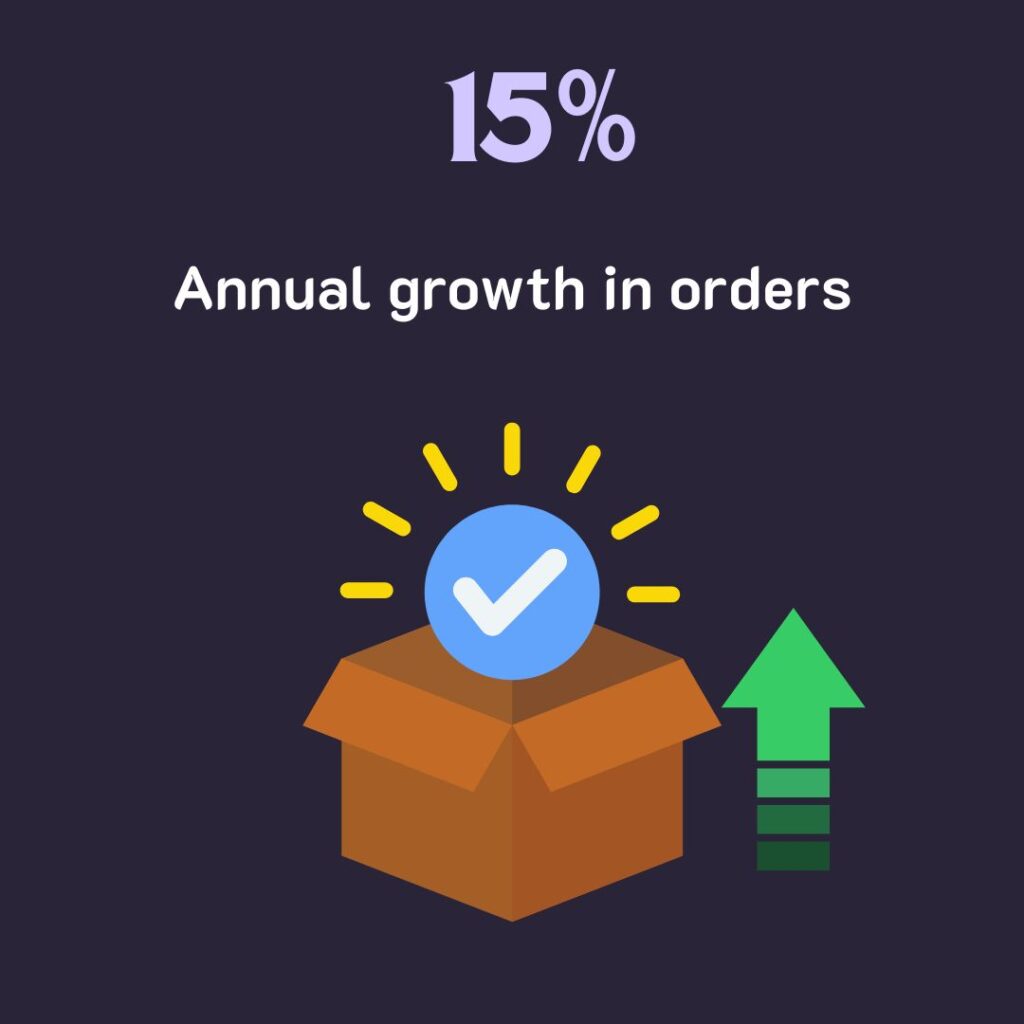
15% annual growth in orders
They were able to cater to the steady 15% annual growth in orders in spite of not buying any new machines..
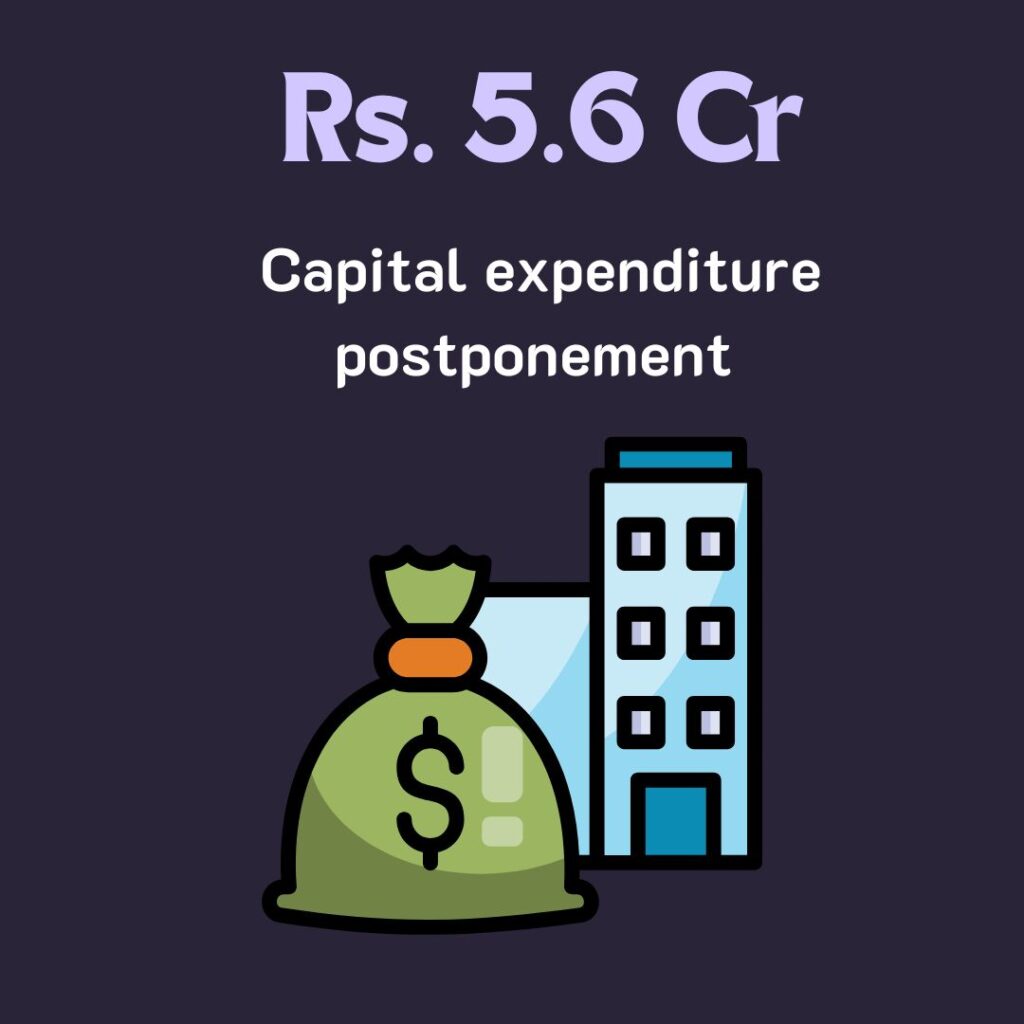
Rs. 5.6 Cr. capital expenditure postponement
Postponement of a significant Rs. 5.6 Cr. capital expenditure for new machines by 2 years, by a freeze on all new machine purchases. They were able to cater to the steady 15% annual growth in orders in spite of not buying any new machines..
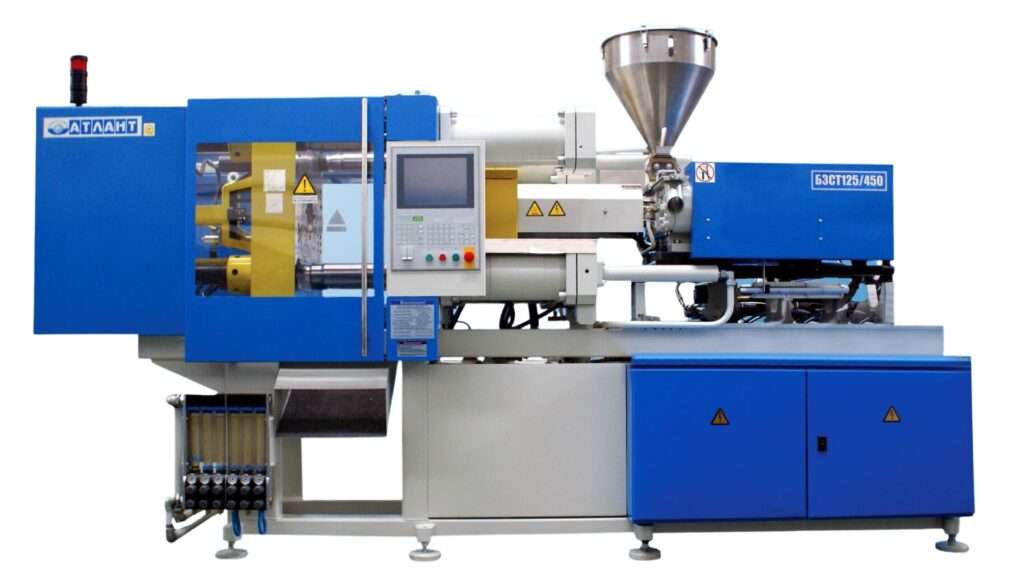
About Customer
Manufacturer of machined castings for export – railway parts and off-road vehicles who operates 56 machines, including CNC lathes, machining centers and foundry equipment. Runs two 12-hour shifts with 1-hour breaks.
Problem
Inefficient machine utilization, that would have necessitated a massive CapEx (capital expenditure) on 18 new machines
Solution
Leanworx efficiently tackled downtime challenges by categorizing issues into two types: low-hanging fruit, quickly addressed through work ethics improvement, and high-hanging fruit, requiring more extensive system changes.
The organization’s team swiftly eliminated low-hanging fruit downtime in a month with a pragmatic mix of incentives. The high-hanging fruit required more time and system adjustments, but Leanworx’s systematic approach and insightful reports, including Pareto charts, enabled a targeted reduction in machine downtime.
Results
The company successfully reduced downtime to 22% within a short span of 5 months, with sustained improvements in the subsequent 2 years.
This achievement led to the postponement of a significant Rs. 5.6 Cr. capital expenditure for new machines by 2 years, by a freeze on all new machine purchases. They were able to cater to the steady 15% annual growth in orders in spite of not buying any new machines.
Increase your profits automatically. Use Leanworx to get accurate and instant data 24/7.
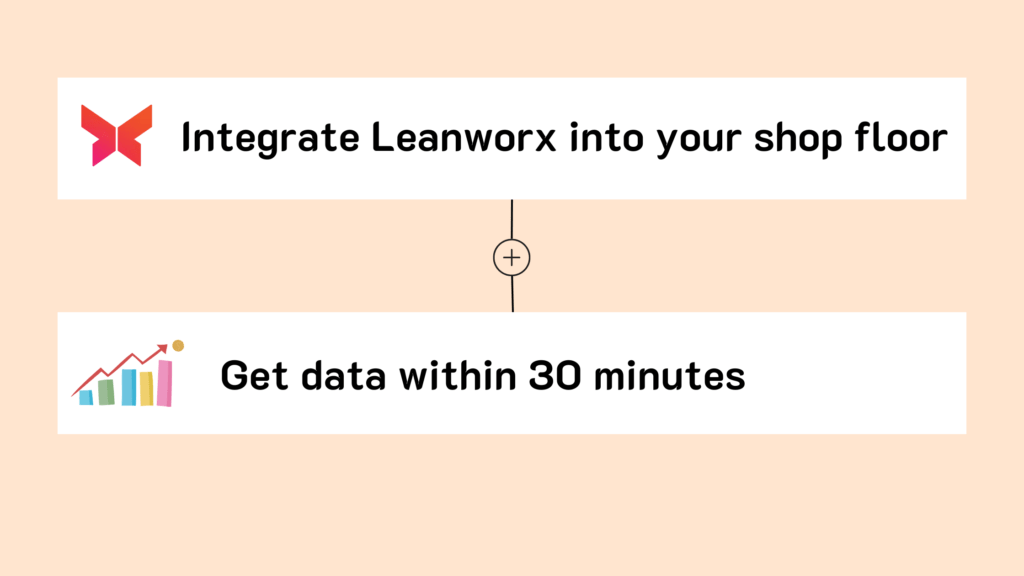